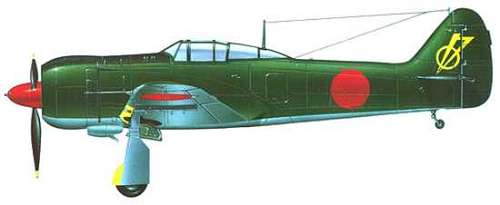

The wing halves are now joined and ready to mate
to the fuse for installation of the hold down bolts. |
 |
The wing saddle sections have been sheeted with 1/8"
balsa and the ply plates installed for the blind nuts. |
After fiber glassing the center section,
the holes are drilled and blind nuts installed. Then seating washers are glued
in place for the wing bolts. | |
 |
Construction of the belly pan starts |
The belly pan is complete |  |

The fuse is fully sheeted and ready
for fiber glassing. While the resin sets, it is time to work on the canopy molds
again. |
 | After
spaying the plugs with cooking oil, the Ultra-Cal 30 is mixed and applied.This
picture shows the first layer being applied approximately 1/8" thick.
|
After the first layer is on, fiber tape is applied to
give the mold strength so it doesn't crack or break during handling.
|  |
 | After
about 30 minutes the final layer is added to make it 3/8" to ½"
thick. After it has cured the plug is removed. |
While the canopy molds are curing, I have begun construction
of the plug for the engine cowl. Seven 16" diameter circles are cut out of
2" pink foam and glued together. Then it is then mounted in my drill press
to act as a vertical lathe. |  |
 |
Only
the front half of the cowl can be done in the lathe since the back must conform
to the firewall shape. |
A masonite firewall template is attached to the back of
the plug. Then I have made shaping tools out of ¾" poplar and attached
self-adhesive 50 grit aluminum oxide sand paper to the edges. The rear of the
plug is then hand sanded to conform to the firewall template. |  |
 | In
this picture the forward cowl ring has been defined, the carburetor air intake
duct has been added, the cannon ports have been sanded out, and final spackling
has been applied. As soon as it is sanded out, it will be ready to be fiber glassed
and primed. |
The foam plugs have been removed from the canopy molds
and now it is time to fill them with Durhams Rock Hard Water Putty. The center
is filled with styrofoam to minimize the amount of putty that is required. After
curing overnight, the plug can be removed and final sanded with foam sandpaper.
|  |

| 040 P.E.T.G is fixed to a frame in preparation for vacuum
forming. The frame will be set in my oven at 150 degrees for about 15 minutes
to remove any moisture from the plastic. Then I turn on the broiler and wait for
the plastic to sag about 2 under the frame before removing to the vacuum
former. |
Plastic pulled down over the frame and formed to
the plug
|  |

| After the canopy is removed, it is cut
down, sanded smooth with an orbital sander, and final sanded with 400 wet/dry
paper. Then a second canopy is pulled over the first to create a totally clear
glass canopy. |
BACK to PROJECTS
|
|
Become an RCWarbrids site supporter by making a donation.
|
$5.00 |
 |
$10.00 |
 |
$15.00 |
 |
$20.00 |
 |
|
|
|
|
|